ANDON系统如何解决重工业车间的信息传递难题
在重工业车间中,生产线的高效运转高度依赖信息的实时性与准确性。然而,传统的信息传递方式(如口头汇报、电话通知)常导致异常响应延迟、信息失真、管理层监控盲区等问题。据统计,因信息传递不畅引发的生产中断,平均每年造成企业15%-20%的效率损失。如何实现从“人找信息”到“信息找人”的转变?ANDON系统的智能化升级给出了答案。
一、ANDON系统:重工业车间的信息中枢
ANDON系统(安灯系统)是一种基于物联网技术的生产异常管理工具,通过实时采集、传递和处理生产数据,构建“异常触发-快速响应-闭环处理”的全流程管理体系。其核心价值在于:
1.异常信息秒级传递:通过传感器、移动终端等设备即时捕捉生产异常。
2.多层级可视化协同:将异常状态同步至车间看板、管理端大屏及责任人终端。
3.数据驱动的持续优化:记录异常处理全流程数据,为精益管理提供依据。
二、破解信息传递难题的四大核心能力
(1)多样化通知渠道:确保信息“零遗漏”
传统车间中,信息传递依赖单一渠道(如广播或纸质单据),易因人员流动或设备故障导致信息丢失。ANDON系统通过以下方式实现全场景覆盖:
1.车间电子看板:高亮显示异常工位、故障类型及处理进度,全员可视。
2.多终端推送:通过短信、邮件、桌面弹窗等方式,精准触达维修人员、班组长及管理层。
3.分级预警机制:根据异常严重程度(如停机风险、质量缺陷)自动匹配通知优先级,避免信息过载。
(2)可视化管理机制:从“黑箱”到透明化
重工业车间设备复杂、工序繁多,管理层难以及时掌握全局生产状态。ANDON系统通过以下功能实现透明化管理:
1.实时监控大屏:展示各产线运行状态、异常统计及处理效率排名,支持远程决策。
2.电子工单追踪:异常处理流程(如报修、派工、验收)全程在线记录,杜绝推诿扯皮。
3.历史数据回溯:通过图表分析高频故障点,针对性优化设备维护计划。
(3)精益化生产赋能从被动响应到主动优化
ANDON系统不仅是异常管理工具,更是精益生产的核心引擎:
1.工位级异常预警:通过传感器实时监测设备参数(如温度、振动),预测潜在故障。
2.生产节拍分析:统计各工位作业周期,识别瓶颈工序并优化排产。
3.数字化看板文化:通过可视化数据培养员工的问题意识,推动持续改进。
三、安灯系统看板选型
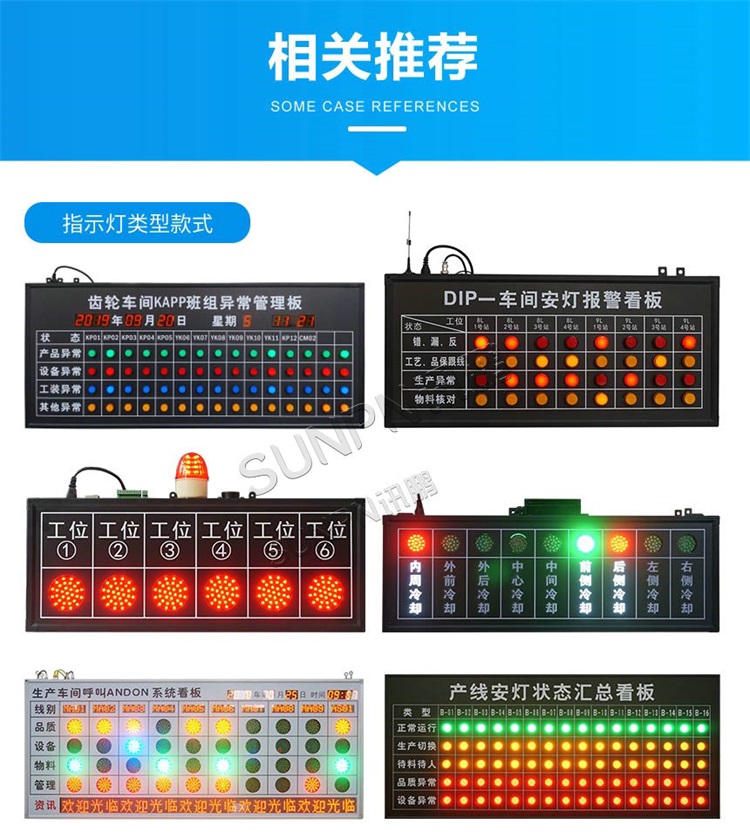
四、重工业车间的数字化转型必经之路
在“中国制造2025”的背景下,重工业车间亟需通过ANDON系统破解信息传递难题,实现生产管理的透明化、敏捷化与数据化。从异常响应延迟到秒级闭环处理,从人海战术到智能协同,ANDON系统不仅是工具升级,更是一场管理思维的革命。
【XF】